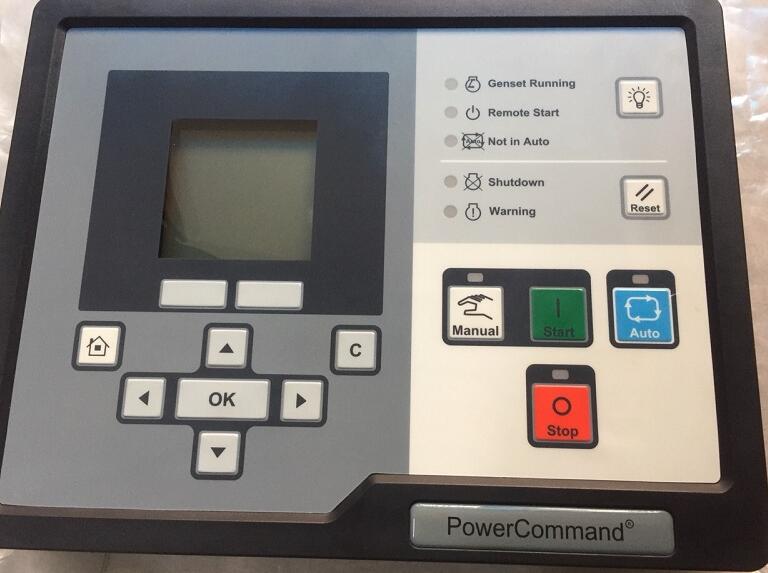
PCC1302 PowerCommand Generator has witnessed a voltage configuration change while generator was in operation.
Preparations:
2024 Cummings InPower 14.5 Pro
PowerCommand Diagnostic 9 Pin Adapter Cable for InPower
Possible Causes:
1 Voltage selection switch was moved during generator operation
2 Open circuit in the voltage position switch harness or connectors
3 Damaged or failed voltage position switch
Diagnosis and Repair:
1 Voltage selection switch was moved during generator operation
a Restart generator and verify operation with switch in fixed position.
b Do not operate voltage selection switch while generator is in operation.
2 Open circuit in the voltage position switch harness or connectors
a Inspect the engine harness and the connector pins.
b Disconnect the engine harness connector from the extension harness.
c Inspect for corroded pins, bent or broken pins, pushed back or expanded pins.
d Inspect for evidence of moisture in or on the connector.
e Inspect for missing or damaged connector seals.
f Inspect for dirt or debris in or on the connector pin.
g Disconnect J20 harness connector from control and voltage selection switch.
h Measure the resistance in each pin from J20 harness connector to the corresponding voltage selection switch terminal. Resistance should be 5 ohms or less.
i. Measure the resistance in each pin from J20 harness connector to ground.
Resistance should be open or infinite.
j. Repair or replace harness as necessary.
3 Damaged or failed voltage position switch
a. Verify switch operation by moving the switch through its range of motion.
b. Visually inspect the selection switch for broken or loose contacts, damage to switch mechanism, rattles or noise when subjected to vibration, and areas that show signs or high heat.
c. Replace switch as necessary.