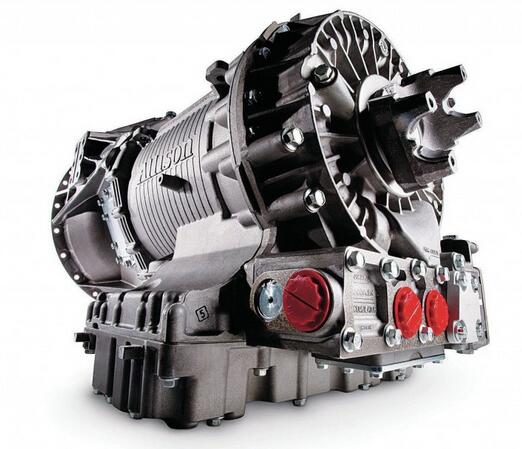
This instruction show you steps on how to solve Allison 3000 & 4000 Gen5 transmission turbine shaft speed sensor circuit P0715.
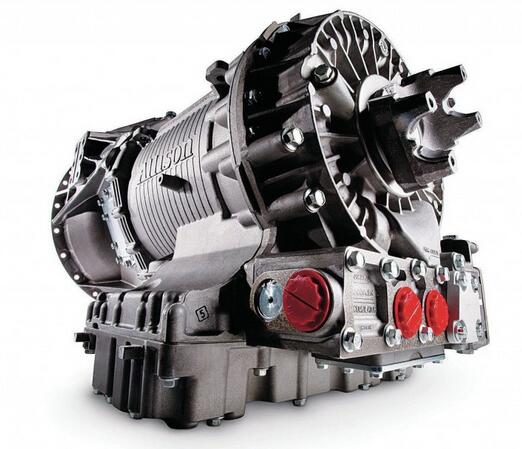
Related Contents:
Allison DOC GEN5 Diagnostic Software 2024.07
2023 Diesel Repair Desktop DTC Solutions V2.9.98+ Diesel Explorer
DIAGNOSTIC RESPONSE:
DNS, Lock in current range
CIRCUIT DESCRIPTION:
The speed sensors are devices which convert mechanical motion to an electrical signal. This test detects a turbine speed sensor circuit short to battery, ground, or open.
ACTION TAKEN WHEN THE DTC SETS:
When DTC P0715 is active, the following conditions occur:
1 If the DTC sets while shift not in process, remains in current range.
2 If the DTC sets while shift is in process, complete shift and lock in that range.
3 There is no response to shift selector requests.
4 DTC is stored in TCM history.
5 The CHECK TRANS light illuminates.
6 The TCM inhibits TCC engagement.
7 The TCM freezes shift adapts.
CONDITIONS FOR CLEARING THE DTC:
Use the diagnostic tool to clear the DTC from the TCM history.The TCM automatically clears the DTC from the TCM history if the vehicle completes 40 warm-up cycles without the DTC recurring.
DIAGNOSTIC AIDS:
DTC P0715 may be caused by:
1 W120 and/or W180 shorted to another wire in chassis harness or to ground.
2 W120 and/or W180 high resistance or open circuit.
3 Broken or defective connector assemblies allowing pushed back pins to short together.
4 Unlocked connectors, missing seal plugs allowing moisture in connectors.
5 Fatigued wires at speed sensor connectors (broken strands).
6 Incorrect pin crimps or expanded terminals.
7 Defective turbine shaft speed sensor.
8Defective TCM.
9 Damaged rotating clutch drum.
10 Wire pair not twisted or not sufficiently twisted.
NOTE:Confirm that the speed sensor wiring consists of twisted pairs at the rate of 12 to 16 twists per 300 mm. These twists must extend the entire length of the wiring harness to within at least 50 mm of the speed sensor connector.
NOTE: The OEM Transmission warranty, or the extended coverage for parts and labor, does not cover transmission or vehicle damage caused by drivelines that do not meet the OEM Transmission specifications.