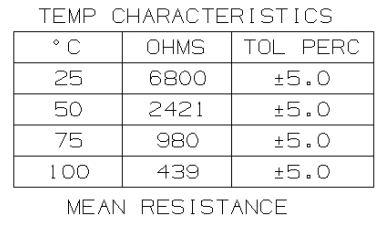
This instruction show you guide on how to solve JCB excavator 140 205 DTC C1024-13 hydraulic temperature sensor open circuit.
Preparations:
2025 JCB ServiceMaster 4 v25.1.0
2017 JCB Parts Plus+ and Repair Service Manual
Possible Cause:
1 Hydraulic oil temperature sensor not connected with the hydraulic oil temperature sensor.
2 Faulty Wire harness.
3 Faulty Hydraulic oil sensor.
Diagnosis:
1 Check wire harness connection with hydraulic oil temperature sensor. Refer below photograph.
2 Check the wire harness connector for terminal back out connecting to hydraulic oil temperature sensor.
3 Check the MECU wire harness connector cavity 3 for 4303D circuit & cavity no 18 for circuit no 4003 for terminal back out.
4 Check the open circuit resistance of hydraulic oil temperature sensor by help of multimeter. The open circuit resistance shall meet the below resistance vs temperature table.
Corrective Action:
1 Replace the faulty wire harness.
2 Correct the terminal back out if any at temperature sensor or MECU END.
3 Replace the faulty temperature sensor.
4